
Manufacturing and Fabrication
CNC Mill | MasterCAM | G.codes | Injection Molding | Lathe
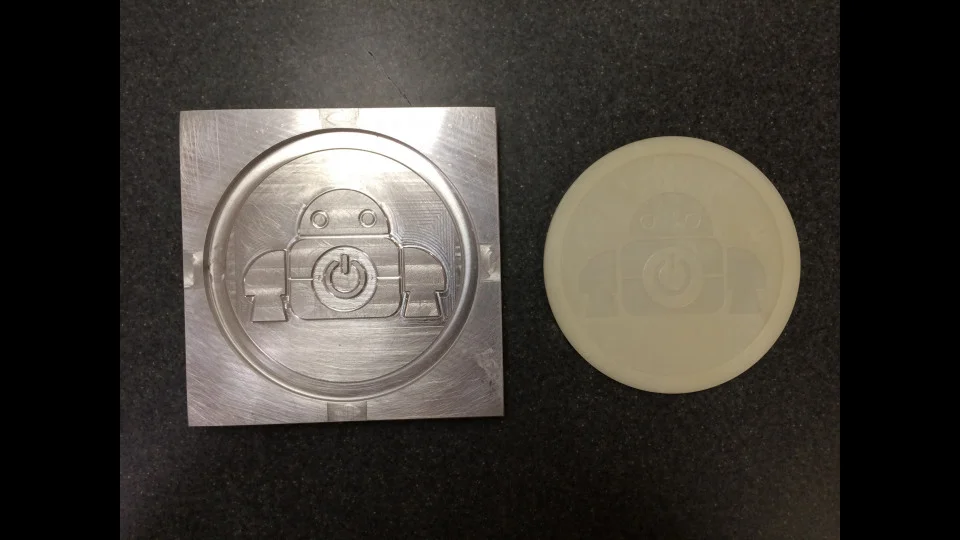
Drink Coaster
I designed and fabricated a custom drink coaster for a Manufacturing course project within specific tolerances and manufacturing specifications.
I began by using thumbnail sketches to explore design options. Once I settled on a design, I modeled the three-dimensional coaster mold in SolidWorks. Using the MasterCAM plug-in in SolidWorks, I created a g-code to be run on a CNC milling machine in Bucknell University's Product Development Lab. After running the CNC to mill a stainless steel coaster mold, I used an injection molding machine to create several prototypes of the coaster design.
I learned the fundamentals of designing for manufacturability on stainless steel molds and plastic parts using SolidWorks. I also developed the ability to program codes for CNC manufacturing equipment. I then gained experience operating CNC and Injection Molding equipment to create rapid prototypes.

Welding Steel Frame
I gained experience with designing, cutting, and welding steel tubing on our BAJA team. The members are 1" and 1.25" OD chromoly steel tubes designed in SolidWorks. The modifications I helped make reduced the weight of the frame by 5%.

Manufacturing Machine Design Improvements
We began the project by visiting our client, Systematic Filing Products LLC, to learn about their manufacturing processes. Using a pain-storming process, we decided on the problem that we wanted to solve. We then designed and modeled a mechanical system that provided a solution to that problem, taking into consideration engineering specifications, cost, ergonomics, safety, and lean manufacturing methodologies.
We decided to address the challenges of a trained worker on the line who had a difficult and ergonomically taxing job of splitting folders into 50 unit piles at high speeds. We created an automated folder separator that used a mechanically actuated pusher rod to guide folders into 50 unit piles at full production speed. The design consisted of a four bar "guidance" mechanism coupled to a cam disk actuator mechanism. Each component was designed by our team to fit the needs of our client based on engineering calculations and a human-centered design process.
This project taught me about the real world applications of mechanical design concepts related to forces, velocities, and accelerations in mechanical linkages. It also developed my skills performing shaft, bearing, and actuation calculations.